THE LOST WAX PROCESS
I use the lost wax method for bronze casting, which has been used since ancient times. Below you will see an illustration of this process in the pieces I produce.
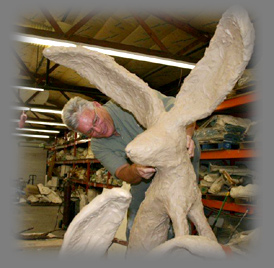
CLAY & RUBBER MOLDS
A mold is made of the original sculpture. The rigid outer mold contains the softer inner mold.--which is the exact negative of the original piece. Inner molds are usually made of latex, polyurethane rubber or silicone. The outer mold can be made from plaster or fiberglass or other materials. Most times molds have at least two pieces. a shim, with keys is placed between the two halves during construction so the mold can be reconstructed accurately. If there are long or irregular pieces sticking out of the original, these are normally cut off and molded separately.
CASTING THE WAX
Once the mold is finished, molten wax is poured into it and swished around until an even coating of about 1/8 inch covers the inner surface of the mold. This is repeated until the desrired thickness is achieved. Another method is filling the entire mold with molten wax, cooling, until the desired thickness is reached on the surface of the mold. After this, the rest of the wax is poured out again and the mold is turned upside down and left to cool and harden.
This hollow wax copy of the original is removed from the mold. This mold may be reused to make multiple copies, as long as the mold remains viable.
Each hollow wax copy is then 'chased'. A heated tool is used to rub out the marks that show the parting line or flashing, where the pieces of mold are joined. The wax is worked to hide any imperfections. The wax now looks like the finished piece. Wax pieces that were molded separately can be heated and attached.
SPRUING
The wax copy is then 'sprued' with a treelike structure of wax that will provide paths fo molten casting material to flow-and air to escape. The careful spruing usually begins at the top with a wax cup, which is attached by wax cylinders to various points on the copy.
SLURRY
A sprued wax copy is dipped into a slurry of silica, then into a sand-like stucco of grain size. The slurry and grit combo is called ceramic shell mold material, all tho it is not made of ceramic. This shell is then allowed to dry, and the process is repeated until a half inch of coating covers the piece. The larger the piece, the thicker the shell needs to be. Only the inside of the cup is not coated. The flat top of the cup serves as the base upon which the piece stands during this process.
BURNOUT
The ceramic shell-coated piece is then placed cup-down in a kiln. The heat hardens the silica into a shell and the wax melts and runs out. Now all that remains of the original work is the negative, formerly occupied by the wax inside the hardened shell.
The ceramic shell is cooled, then tested to see if water will flow thru the vent tubes. Cracks or leaks can be patched at this point with paste.
POURING
The shell is then reheated in the kiln to harden the patches and remove all moisture, then placed cup-up into a tub filled with sand. Metal is melted in a crucible in a furnace, then poured into the shell. The filled shells are allowed to cool.
The shell is then hammered or sand-blasted away, releasing the rough casting. The spruing, which are also recreated in metal, are cut off, to be reused in another casting.
METAL CHASING
The casting is then worked until all signs of the process are removed and the casting looks like the original. All defects, air bubbles or pits are filed down and polished at this point.
PATINA AND BASE ATTACHMENT
The patina chemicals are sprayed or hand applied in several coats then heated and cooled. After cooling the finished piece is then
given a wax coating to preserve the finish.
The mounting is done on marble ,wood, glass or the piece can be a stand alone with felt on the smooth bottom.
|